12 July 2025
Have you ever wondered how some companies seem to always be one step ahead? How they manage to stay flexible, efficient, and competitive even in the face of constant change? The answer often lies in one powerful concept: continuous improvement.
It might sound like a buzzword, but continuous improvement is far more than that. It’s a mindset. It’s a culture. And for businesses that want to thrive—not just survive—it’s a must-do. In this article, we’re going to break down what continuous improvement really is, why it matters so much in operations, and how you can start applying it to your own business. So grab a cup of coffee and let’s dive in.
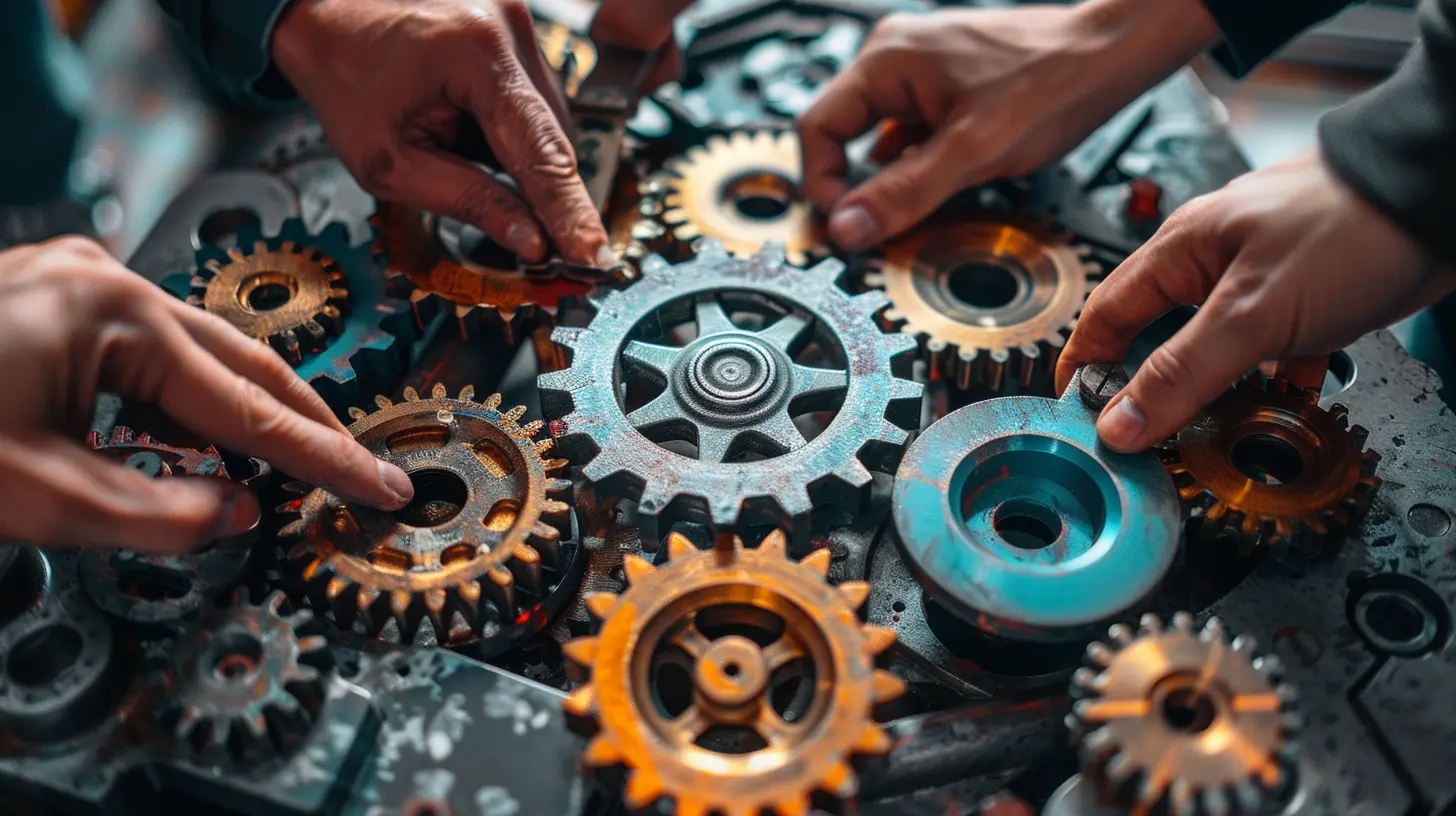
What Is Continuous Improvement, Really?
Let’s not overcomplicate things—continuous improvement simply means getting a little better each day. It’s the ongoing effort to enhance products, services, or processes. The core idea? Don’t settle. There’s always room for improvement.
Think of it like tuning up a car. Even if your vehicle is running well today, small tweaks can help it run smoother, use less fuel, and last longer. Businesses operate in much the same way.
In operations, continuous improvement involves analyzing how things are done, pinpointing inefficiencies, and then making small—but meaningful—changes to boost performance over time.
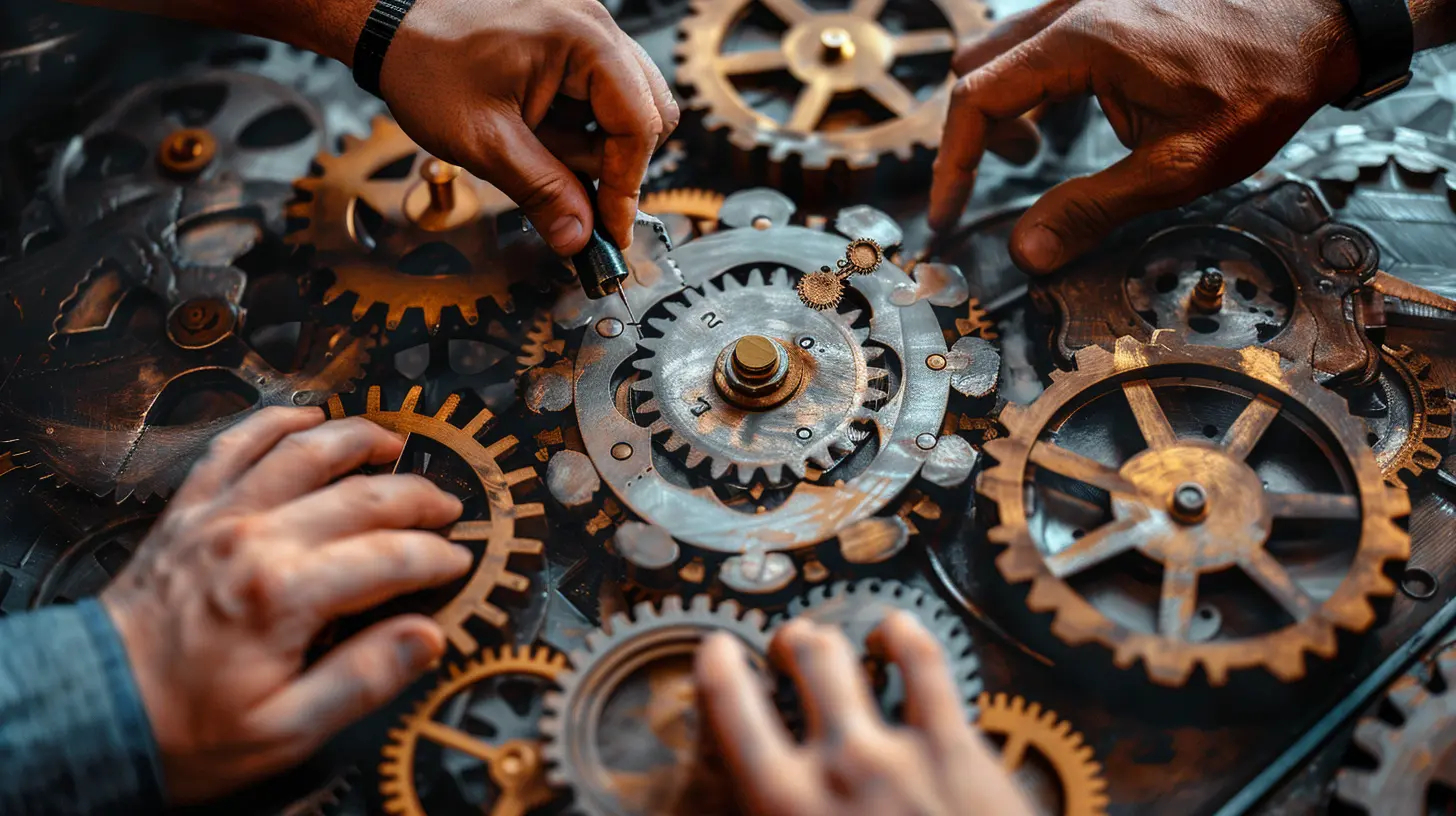
Why Should Operations Even Care?
Operations are the backbone of any business. They’re where the actual work gets done—producing goods, delivering services, managing supply chains, processing orders, and so on. If your operations aren’t efficient, your business is going to feel it—hard.
Here are a few solid reasons why continuous improvement should be on every operations team’s radar:
1. Competitive Advantage
Let’s be honest—the business world is cutthroat. Customers have options, and if you can’t deliver quickly, reliably, and at a good price, they’ll go elsewhere. Continuous improvement allows you to streamline your processes and stay agile, so you can respond faster and better than your competition.
2. Cost Reduction
You’d be amazed how much money businesses waste due to inefficiencies. We're talking about unnecessary steps in a process, too much inventory, or even poor communication. Making small improvements can help plug those money leaks and improve your bottom line without slashing budgets or laying off workers.
3. Employee Engagement
Here’s a fun fact: people love being part of something that grows and gets better. When employees are encouraged to contribute ideas and help improve how things are done, they feel valued. This leads to higher morale, lower turnover, and a culture of innovation.
4. Improved Quality
When you continuously refine your processes, you naturally reduce mistakes and defects. This means better-quality products or services and, ultimately, happier customers. What’s not to love about that?
5. Customer Satisfaction
Speaking of customers—when your operations run smoothly, it shows. Orders arrive on time, products work as promised, and service is top-notch. That keeps customers coming back and spreading the word.
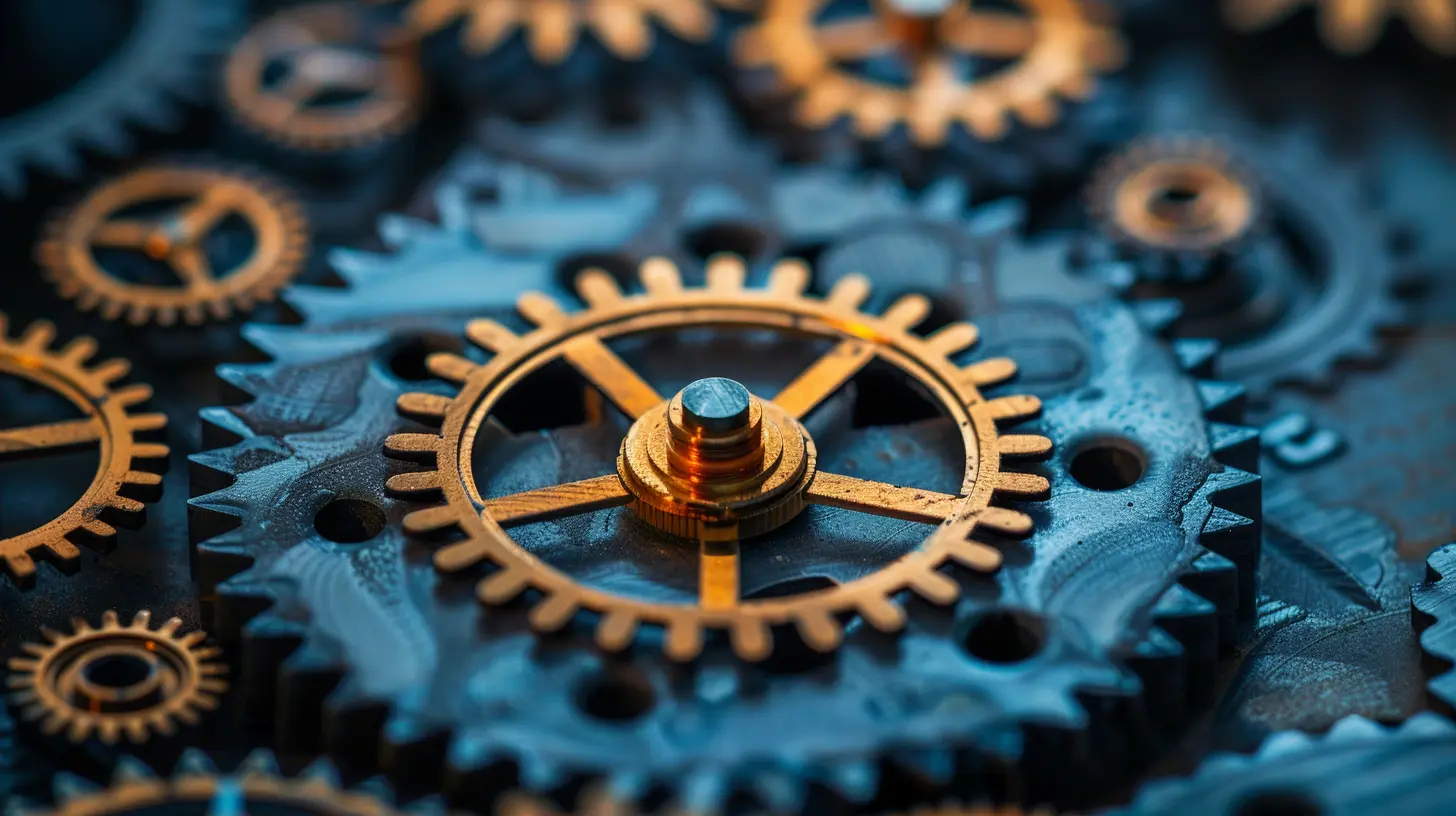
The Pillars of Continuous Improvement
Not all improvement strategies are created equal. Some are overly complicated. Others don’t stick. To make your efforts count, it helps to understand the key principles behind effective continuous improvement.
📌 Kaizen Thinking
Kaizen is a Japanese term that means “change for better” or “continuous improvement.” The idea is simple: everyone, at every level of the organization, is responsible for making small, regular improvements.
Kaizen is more of a habit than a one-time fix. It’s about fostering a mindset where you’re always asking, “How can we make this better?”
📌 Data-Driven Decisions
Guesswork is out. Continuous improvement relies on data to uncover where things are going wrong and how to fix them. Think metrics, KPIs, customer feedback, and process mapping. You can’t improve what you can’t measure.
📌 Standardization
Ironically, to improve, you need some consistency first. Standardizing processes helps you identify what’s working and what’s not. Once you’ve made improvements, those new best practices become the new standard. Rinse and repeat.
📌 Employee Involvement
Your frontline employees often have the best ideas for improvement because they live and breathe the processes daily. Ignoring their insights is like driving with a blindfold on. Empower them, listen to them, and include them in the improvement journey.
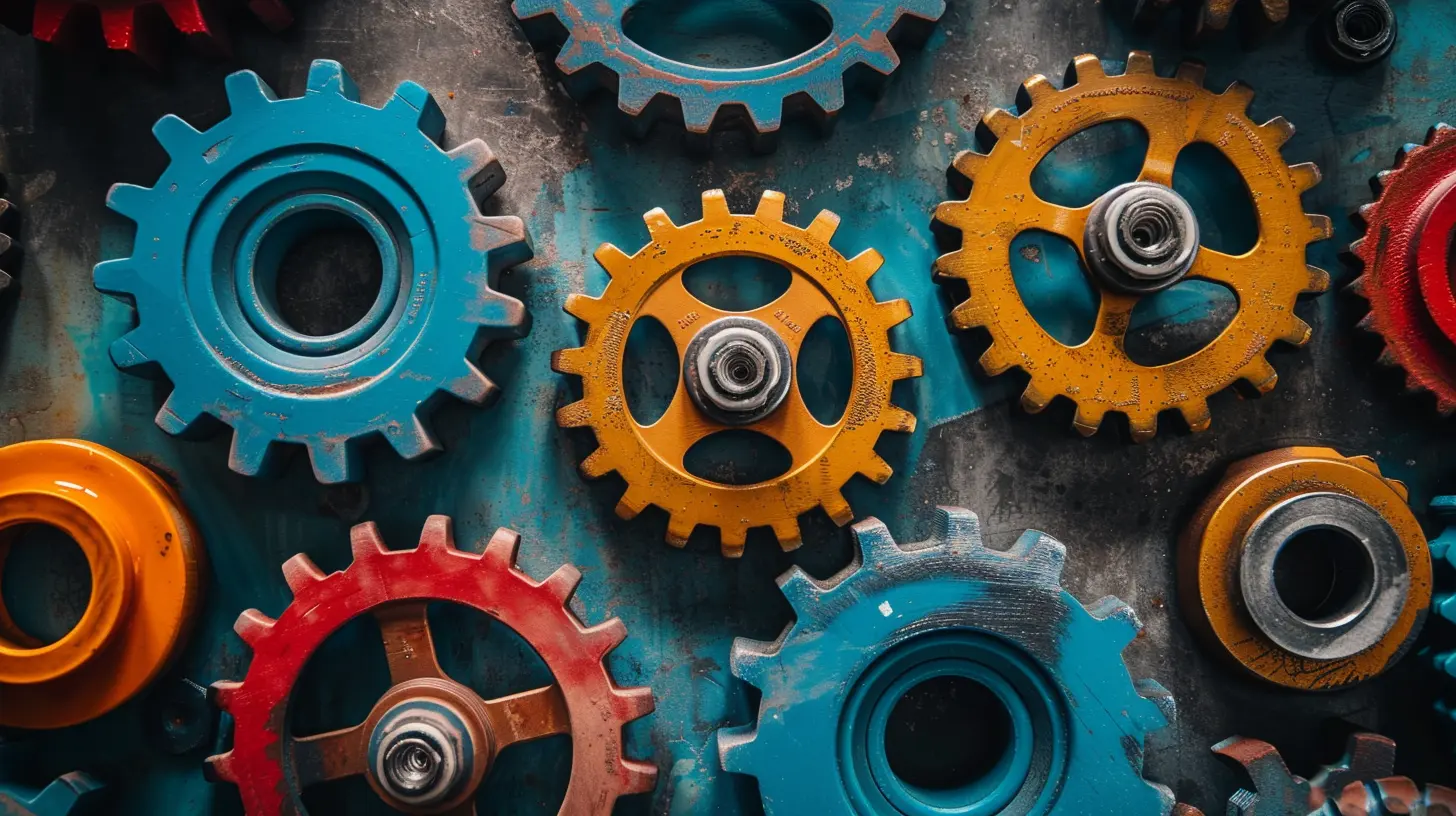
Common Continuous Improvement Tools
Let’s dig into the toolbox. Here are some go-to methods that can support your continuous improvement efforts:
✅ PDCA Cycle (Plan-Do-Check-Act)
- Plan: Identify an area for improvement, set goals, and plan your strategy.
- Do: Implement the change on a small scale.
- Check: Measure the results and see if it worked.
- Act: If it worked, standardize it. If not, adjust and try again.
It’s like a mini feedback loop that keeps turning.
✅ Lean
Lean is all about doing more with less. That means cutting waste—whether it’s time, materials, or effort. Lean doesn’t mean cheap; it means efficient. Think of it as trimming the fat but keeping the muscle.
✅ Six Sigma
This one’s a bit more technical. Six Sigma uses statistics and data analysis to reduce variation and defects. If you’re all about precision and perfection, this is your jam.
✅ 5S System
Sort, Set in Order, Shine, Standardize, Sustain. This system helps you organize workspaces to improve efficiency and safety. It’s like spring cleaning, but all year long.
Real-World Examples of Continuous Improvement
Sometimes the best way to understand a concept is through real-life examples. So let’s look at a few businesses that nailed it with continuous improvement.
Toyota
Toyota is practically the poster child for continuous improvement. Their “Toyota Production System” is built around Kaizen, and it’s helped them become one of the most efficient and respected car manufacturers in the world.
Employees at all levels are encouraged to spot inefficiencies and contribute ideas. No improvement is too small. That commitment to ongoing change is a big reason for Toyota’s lasting success.
Amazon
Love it or hate it, Amazon is a master of operations. Their relentless focus on efficiency—whether it’s in their logistics network, warehouse layout, or delivery processes—is all thanks to continuous improvement practices.
They’re constantly testing, measuring, and fine-tuning to shave off seconds and save costs, all while improving customer experience.
Starbucks
Even your morning coffee benefits from continuous improvement. Starbucks invests heavily in training, process optimization, and customer feedback loops. They refine everything from how baristas move behind the counter to how inventory is tracked, ensuring a consistent and fast service.
How to Get Started with Continuous Improvement
Ready to roll up your sleeves? Here’s how you can start embedding continuous improvement into your operations.
1. Start Small
You don’t need to flip the table on day one. Pick one process that needs work and focus on improving it. Think of it like learning guitar—you start with one chord and build from there.
2. Get Everyone Involved
Make it a team thing. Encourage employees to share feedback, point out inefficiencies, and suggest solutions. The more brains in the room, the better the ideas.
3. Use the Right Tools
We talked about PDCA, Lean, and Six Sigma for a reason. These tools work. Pick one that fits your business size and complexity and start experimenting.
4. Measure Everything
Keep track of what you’re doing. Are you saving time? Reducing costs? Boosting quality? Use KPIs and data to validate your efforts and tweak as needed.
5. Make it a Habit
Remember, continuous improvement isn’t a one-and-done project. It’s a mindset. Set regular check-ins, hold retrospectives, and celebrate wins—no matter how small.
The Future Belongs to the Agile
Let’s face it—change is the only constant. Customer expectations evolve. Markets shift. Technology never stops advancing. If you’re not improving, you’re falling behind.
That’s why continuous improvement in operations isn’t just “nice to have.” It’s a competitive necessity. It keeps your business nimble, your employees engaged, and your customers satisfied.
But here's the truth: it’s not always easy. It takes commitment, patience, and a willingness to question the status quo. But once the wheels start turning, the results speak for themselves.
So the next time you're reviewing your operations, ask yourself: what can we improve today?
Bonus: Continuous Improvement in Remote and Hybrid Work
Yup, you guessed it—continuous improvement isn’t just for the factory floor or service counter. Many companies now operate remotely or in hybrid models, and they, too, need to keep evolving.
From optimizing Zoom meetings to refining project management tools like Asana or Trello, there’s always something that can be made smoother. Even digital workplaces need decluttering and polishing.
And don't forget communication. Clearer messages, faster responses, less back-and-forth. A culture of constant tweaking can make a massive difference, no matter where your team is located.
Final Thoughts
Continuous improvement in operations is like compound interest for your business. Small gains, multiplied over time, lead to massive progress. The best part? It's accessible to everyone. Whether you're running a startup, a manufacturing plant, a digital agency, or a coffee shop—there’s always something you can improve.
So go ahead, take that first step. Your future self—and your customers—will thank you for it.